Well, after much deliberation and in receiving some really good advice and tips from Waytec, I have decided to change my approach to all this. I have now moved the pressure switch to the tank, as well as the check valve. Up front comes the fun stuff! I have decided now to convert my Sanden compressor to run on grease. A lot of reading has given me enough confidence that if I kill it, then its easy and cheap enough to replace with another one. Now the fun begins!
I went to the wrecker the other day to look for a spare compressor that would fit so I could at least work on it and keep my jeep drivable. I found a suitable one on a 98 that was in a front end smash, but the engine was still intact, and it even had a brand new alternator on it! Double score! I have finally had a chance to take the compressor apart to begin the conversion and found that it was a darn good thing that I did, as at the top of one of the pistons, there was a small piece of metal that must have come loose, or was dropped in there from the factory when it was made. It wedged between the head and the flapper valve, in turn damaging the piston and breaking off a piece of the flapper valve

This is however easily replaced from what I can tell, and when I finally take my old compressor out of my jeep, I will likely just rob the parts that I need from that one to make one good one again. Now all I have to do before I can switch to grease is to drill out and tap an oil passage inside the compressor to keep the grease inside it and out of my air lines, and then fitting some standard NPT fittings to a non standard compressor head! I scratched my head over this for a few hours tonight, but I think I have figured this one out. The tapping of the oil galley is fine, and I will just thread lock a small set screw inside it to block most of the grease from getting out. The other part I had to think about though was how to get a standard air fitting to mate to the head. For the intake side, it doesn't seem like it will be a big deal as there is no pressure against it, so I'm just going to put a filter onto the end of the original air line. However the discharge side will prove to be a problem.. This side seems like it is too shallow to get enough threads out of a tap. After staring at the head for about an hour, and enjoying an ounce of 15yr old single malt, I finally came up with an idea! On the back of this one there is a pressure relief valve, which my XJ does not have! To my delight, it is a standard thread that I already have a tap for. I think tomorrow I am going to just drill out the center hole where that pressure relief was, and tap that to 1/4 NPT for the discharge fitting, and then up top on the old discharge port, I will cut off and grind down the o-ring pad, and re-tap into the existing hole to take the pressure relief valve! Problem solved! I don't have to drill any more holes into the head, or block any other ports. Thankfully, with this head being slightly different than the one on the jeep, it just worked out better!
So far so good! Also managed to finally get the tanks mocked up in the back of the jeep, where they tuck in nicely out of the way into the rear corner. I hope to get some brackets fabbed up to attach it securely, and then I can work on more mock up, and plumbing the lines!
More pictures of the progress thus far!
This shows the damaged piston, from the manufacturing defect...
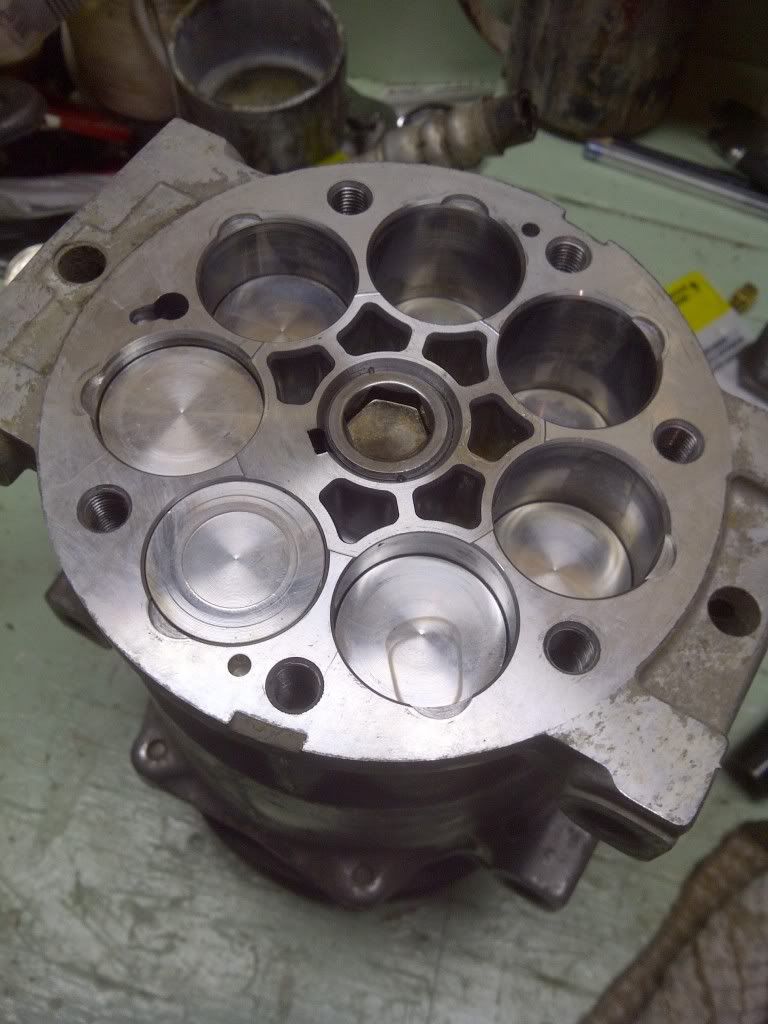
The small piece of metal that was stuck to the head under the flapper valve
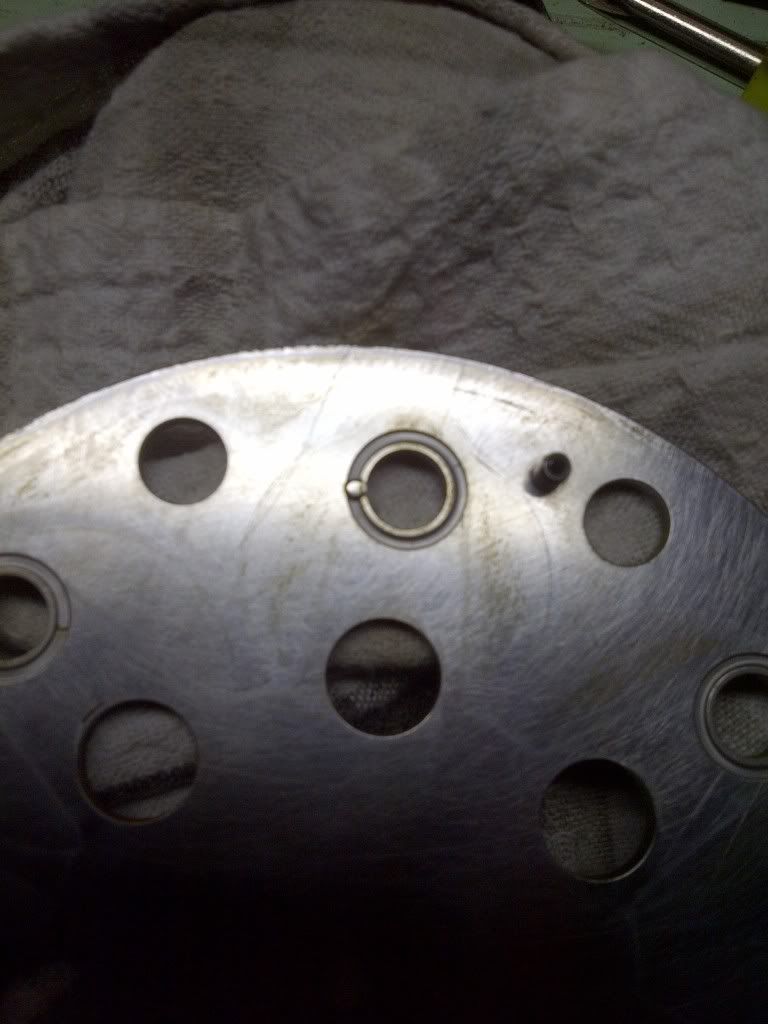
And the broken flapper valve
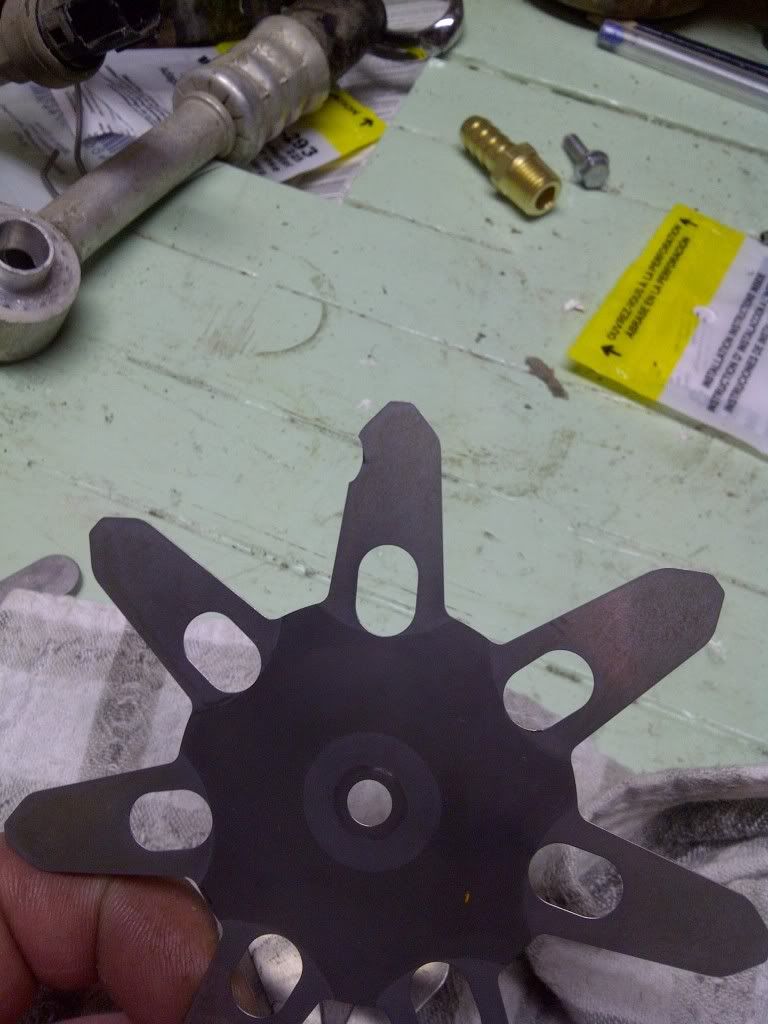
Here is the head that I will modify in a few days time, removing the o-ring pad on the right side, and tapping that small hole to accept the pressure relief
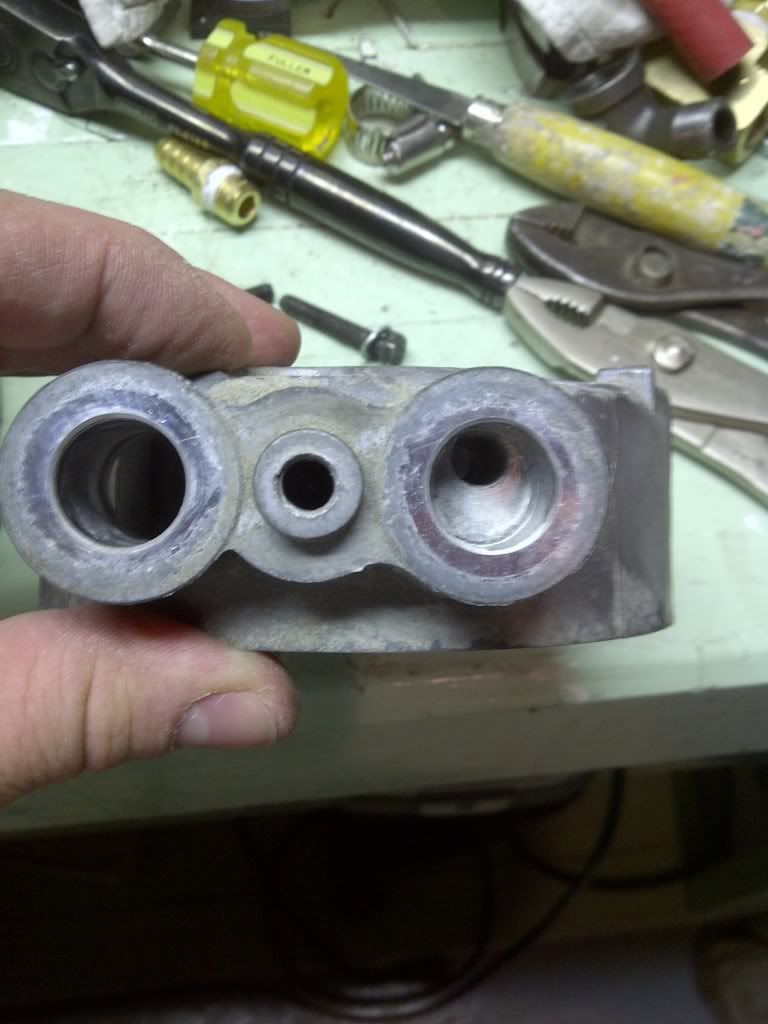
And the mock up of what I plan to do after its tapped. That center hole will be tapped to accept a standard NPT fitting
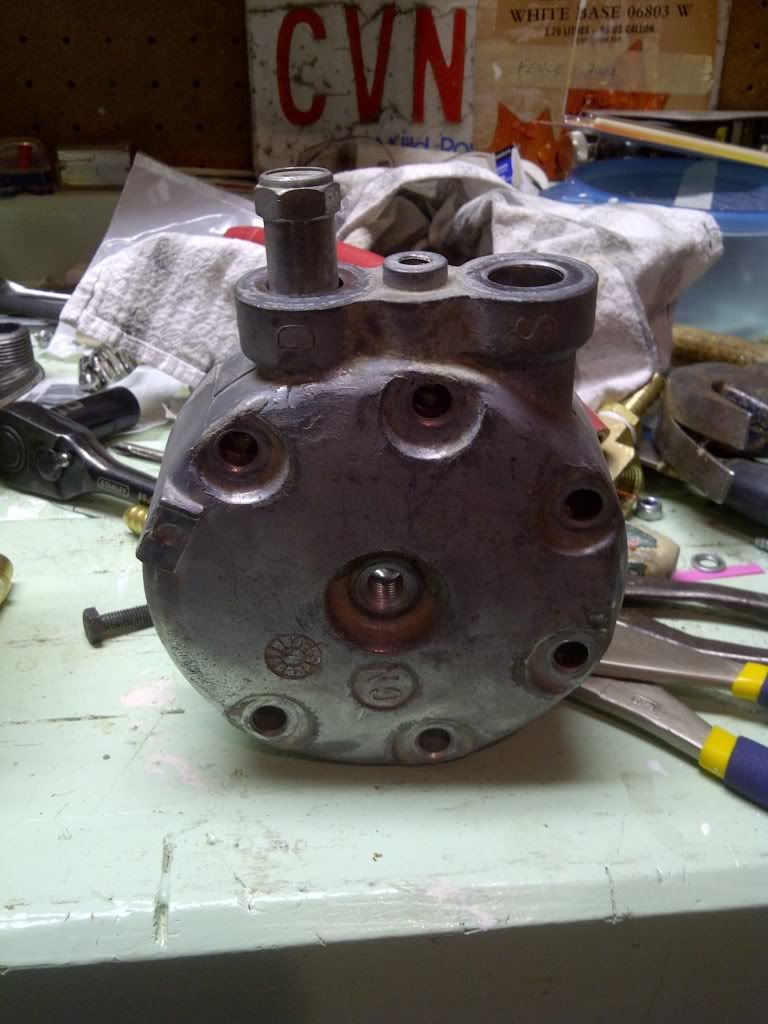
This is the inside of the head, The outer chamber is where the suction occurs for intake, and the center chamber is discharged through the hole in the top right. The center was originally the pressure relief, but that will be swapped out for a more simplistic approach to plumbing standard fittings to it.
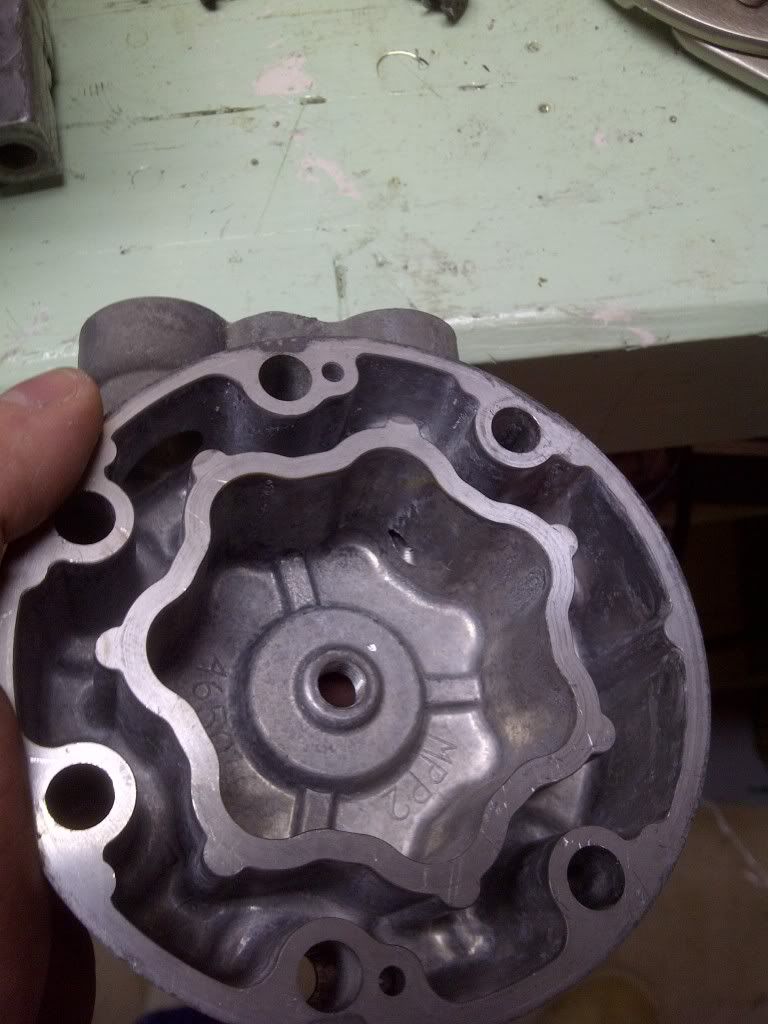